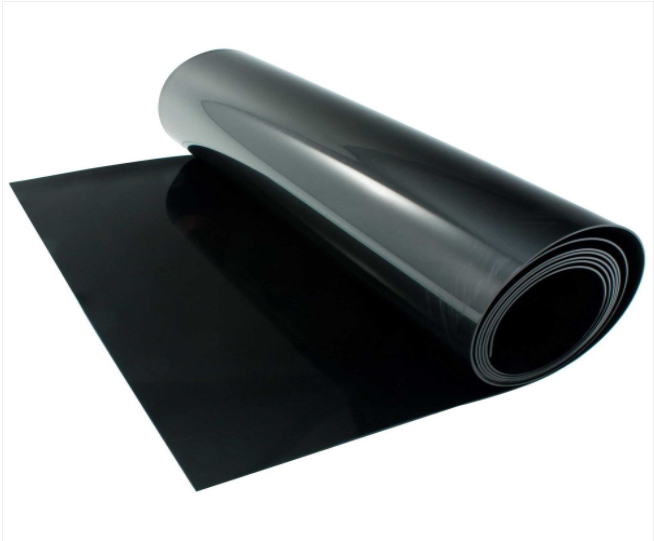
The production process of industrial rubber sheet involves multiple steps,technologies,and materials,making it a complex process in modern industrial production.This process not only requires extremely high precision and strict quality control,but also careful consideration of environmental impact.In this article,we will explore the production process of industrial rubber sheet,from raw materials to final products,step by step.
1.Raw Material Preparation
The foundation of industrial rubber sheet production is high-quality raw materials,including raw rubber,auxiliaries(such as sulfur and accelerators),and fiber and metal materials that may be used.The choice of these materials directly affects the quality and performance of the rubber sheet.In this stage,it is important to ensure that all raw materials meet the needs of high-quality production.In addition,the storage of raw materials should follow strict regulations to avoid the impact of environmental factors(such as temperature and humidity)on material performance.
2.Compounding and Mixing
The purpose of compounding is to increase the plasticity of rubber,making it easier to process.This process typically involves high temperatures and mechanical action,which changes the long-chain molecular structure of rubber physically to obtain the desired plasticity.
Mixing,on the other hand,involves mixing the plasticized rubber with various auxiliaries to achieve the desired physical and processing properties.In the mixing process,uniformly dispersing the auxiliaries is crucial,which directly affects the uniformity and quality of the rubber sheet.
3.Calendering and vulcanization
After the rubber has been mixed,it will be formed into the desired shape,which is called calendering.Depending on the product requirements,rubber can be formed into sheet or specific shapes through calendering or molding.Calendering not only gives the rubber its shape,but also prepares for the subsequent vulcanization process.
Vulcanization is the core step in the production process of rubber products,which converts the thermoplastic rubber into a thermosetting material through a chemical reaction,thus obtaining excellent mechanical properties and stability.During the vulcanization process,controlling the temperature and time is the key to ensuring product quality.
4.Finishing and inspection
After vulcanization,the rubber sheet will be cooled and trimmed to remove excess material and ensure precise dimensions.Then,the product will undergo rigorous quality inspection,including but not limited to visual inspection,dimensional measurement,and physical property testing.Only products that pass these tests completely can be considered qualified products and then packaged and sent to the market.