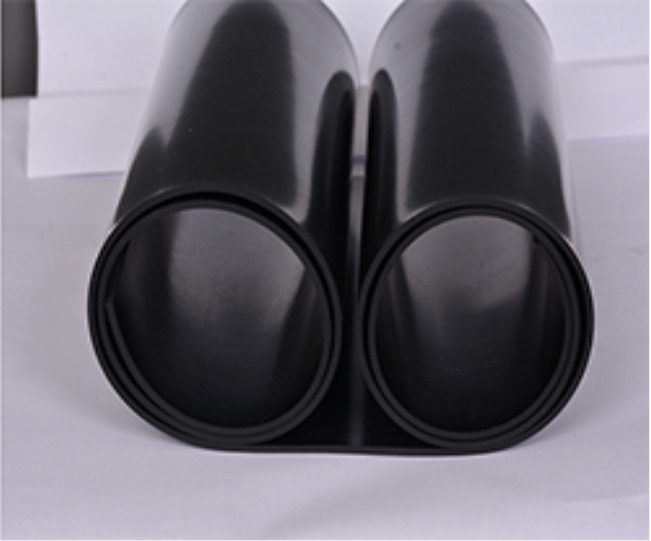
EPDM rubber rolls, also known as three-component EPDM, are a type of synthetic rubber made by copolymerizing ethylene, propylene, and a small amount of a third monomer. It is renowned for its excellent weather resistance, resistance to ozone, and electrical insulation properties. These characteristics make EPDM an ideal material for manufacturing various products, such as automotive parts, electrical wires and cables, and rubber products.
How are EPDM rubber rolls produced? The production process can be divided into two main stages: the production of raw materials and the synthesis of EPDM rubber rolls. In the raw material production stage, we need petrochemical raw materials such as butadiene rubber, high-purity nitrogen, hexene, ethanol, ethylene, and propylene. These raw materials undergo a series of chemical reactions, ultimately synthesizing EPDM rubber rolls.
Let’s now look at the main application areas of EPDM rubber rolls.
In the automotive industry, EPDM rubber rolls are widely used to manufacture window seal strips, tires, and pipes. This is because EPDM rubber rolls have excellent weather resistance and heat resistance, and can withstand extreme temperature changes and ultraviolet light exposure. Additionally, EPDM rubber rolls have good electrical insulation properties, making them widely used in the electronics industry, such as the protective layer of electrical wires and cables.