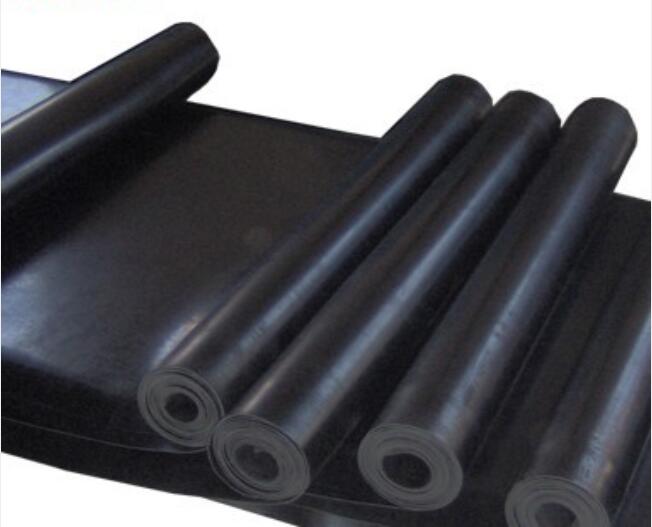
The production process of neoprene rubber mainly includes the following steps:
Material preparation:The first step is to purchase chemical raw materials,including monomers such as chloroprene,styrene,and acrylonitrile,as well as initiators and emulsifiers as auxiliaries.Of these,chloroprene is the main monomer,and styrene and acrylonitrile are used to regulate the properties of the rubber.
Emulsion polymerization:The above raw materials are added to the emulsion in a certain proportion and subjected to emulsion polymerization reaction.The specific operation steps include adding the monomers and auxiliaries to the emulsifier to form a stable emulsion system,then adding the initiator to initiate the polymerization of the monomers to form neoprene rubber particles.
Coagulation and drying:After the emulsion polymerization is completed,the coagulation and drying treatment is needed to obtain the finished neoprene rubber.The operation steps include adding a coagulant to the emulsion to coagulate the neoprene rubber particles into block-shaped particles,then drying the block-shaped particles to obtain the finished neoprene rubber.
Post-treatment:In order to improve the properties of neoprene rubber,some post-treatment operations are needed,such as adding anti-aging agents,antioxidants,etc.to improve heat resistance and aging resistance;or vulcanization treatment to improve mechanical properties and chemical resistance.Additionally,the production of neoprene involves the operation of spreading zinc stearate on the surface of the rubber in a closed device to ensure the sanitary conditions of the working environment and prevent dust flying and pollution.During vulcanization,neoprene can be vulcanized in the same way as other general-purpose rubbers,but the vulcanization temperature needs to be slightly higher than that of natural rubber,preferably above 150°C.During vulcanization,it is necessary to pay attention to the process problems of sticking to the mold and rotten eye,and take corresponding measures to solve them.