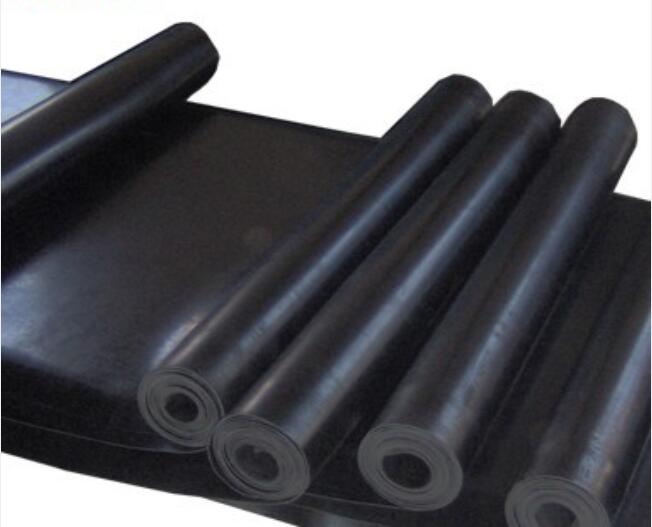
In modern industrial production,the application of thin rubber sheets is becoming increasingly widespread,from simple gaskets to complex industrial applications.This material is highly valued for its unique properties.However,producing high-quality thin rubber sheets is not an easy task,as it involves a series of complex and delicate production processes.
Let’s start with the mixing process,which is the first step in rubber processing and is also a key factor in determining the quality of rubber products.The purpose of mixing is to evenly mix the raw rubber with various auxiliary agents to improve its plasticity and lay a foundation for subsequent shaping and vulcanization.
Mixing can be divided into open-coiler mixing and closed-coiler mixing.Open-coiler mixing is a more traditional mixing method that relies on the mixing of rubber and auxiliary agents by two rotating rollers.During operation,strict control must be exercised over factors such as the amount of rubber added,the order of adding materials,the gap between rollers,and roller temperature.In comparison,closed-coiler mixing is carried out in a closed environment and can more effectively control the temperature and pressure of the material,making it suitable for large-scale production needs.
Next is the calendering process,which is crucial for the production of thin rubber sheets.
Calendering is the process of producing specific thickness rubber sheets or semi-finished rubber cloth products by rolling the already mixed rubber through a calender.In the calendering process,the appropriate temperature and speed need to be adjusted according to different types of rubber,such as natural rubber,styrene-butadiene rubber,chloroprene rubber,ethylene-propylene rubber,and nitrile rubber,to accommodate their different thermoplasticity and shrinkage.For example,natural rubber is easy to calender and bond,but care must be taken to control the temperature difference between the rollers to facilitate the transfer of the sheet;while nitrile rubber has a high shrinkage rate,it needs to be filled or softened with softeners to reduce the shrinkage rate.
In the production of thin rubber sheets,various problems may arise,such as rubber adhering to the rollers,air bubbles forming,and rough surfaces.These problems can usually be solved by adjusting the formula and improving the process conditions.For example,reducing the adhesion of rubber to the rollers can be achieved by adding specific demolding agents or adjusting the temperature of the rollers.To avoid the formation of air bubbles,the mixing process can be optimized to ensure that the gas in the rubber mixture is fully expelled.