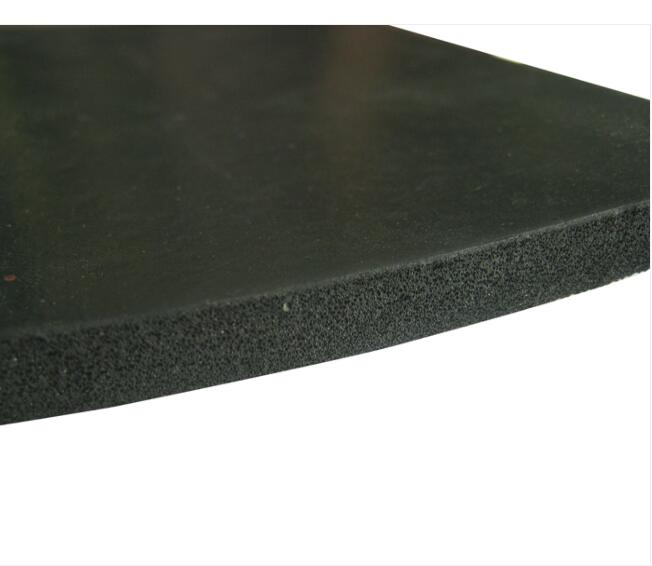
The production of sponge rubber cannot be separated from a critical process-the formation of rubber sponge.This process begins with the spongeing of solid rubber,with the core being the addition of a spongeing agent to selected rubber compounds.As the vulcanization temperature rises,the spongeing agent begins to decompose and releases gas,which is surrounded by the surrounding rubber and forms bubbles,causing the rubber to expand into a sponge-like structure.The factors that determine the pore structure include the spongeing agent’s gas generation,the diffusion speed of gas in the rubber,the viscosity of the rubber,and the vulcanization speed,of which the most critical is the matching between the spongeing agent’s gas generation and the generation speed of gas with the vulcanization speed of the rubber.
In the production of sponge rubber,selecting the right type and size of spongeing agent is crucial.This not only affects the spongeing efficiency but also directly affects the quality of the final product.For example,for applications that require high elasticity and softness,such as sports shoe soles,a spongeing agent that can produce large and evenly distributed open-cell sponge is needed.For applications that require good sealing performance,such as sealing strips for automotive windows,a spongeing agent that can produce fine and even closed-cell sponge is needed.From basic materials science to complex manufacturing processes,every step requires careful design and strict control to ensure that the final product can meet the increasingly demanding performance requirements.
With the development of new materials and technologies,the application range of sponge rubber will become more extensive in the future,and its role in improving people’s quality of life and driving industrial progress cannot be underestimated.